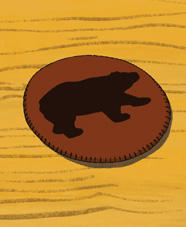
I’ve been making and selling leather goods full-time at my store and blackbearleather.com since 2016. Black Bear is named for the construction business my father and Amish grandfather started out of the family barn in 1972.
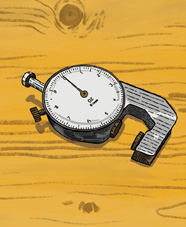
A leather weight gauge helps us measure 3 ounces, or 3/64-inch thickness, for wallets; 6 ounces for journals; and 12 ounces for belts.

It takes about an hour to hand-stitch each wallet. The saddle stitch method locks in the waxed thread.

Rotary strap cutters make a clean cut of any width. I can crank through five 1–1/2 inch belt straps at once.
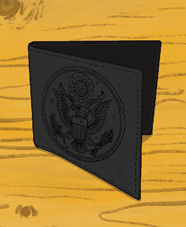
Black Bear made the official wallets for members of the 117th Congress. We stitched 375 between mid-August and Election Day.

The notched blade of a beveler removes the leather’s hard corners. The rounded edges are then dyed and burnished with a wooden slicker.
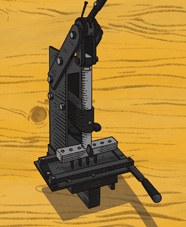
When I first started making belts, I measured and punched all 13 holes individually. A self-centering belt press takes care of that in one pull.
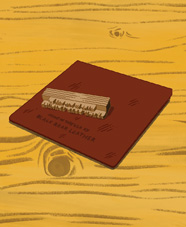
I source our leather domestically. Tanneries in India and China use chromium sulphates, industrial chemicals that pollute rivers.

Nonfiction books and sci-fi epics on Audible keep my brain active when I’m doing monotonous stitching work.
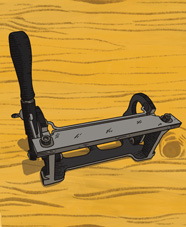
Skiving blades shave down the thickness of leather, like on the buckle end of belts.

I grew up building sheds with my dad and three brothers and have always carried a utility knife. It’s the primary tool I use today.
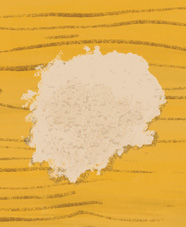
Wickett & Craig in Pennsylvania tans our leather by soaking hides in a bath of vegetable tannins, derived from tree bark, for two to three weeks.
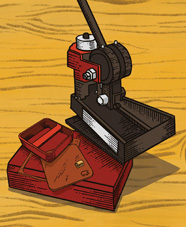
A clicker is a real time-saver, cutting out die pieces like coasters and embossing our logo onto the leather.
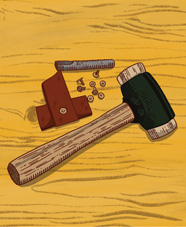
A mallet strikes a rivet setter to lock a copper rivet in place. I’ll do 20 to 30 a day if I’m making tote bags.

A skylight in my workshop makes it feel comfier and feeds my 22-houseplant jungle.